Manufacturer of Food Service Equipment Improves Laboratory Process.
To improve efficiency at a major manufacturer of food service equipment, a SIPOC model was used to define a complex laboratory process. At the company, recent management changes necessitated the need for change within the organization, which included a strategic goal of doubling sales within the next 6 years. Many of the processes; however, were not documented, and therefore, were not reproducible and lacked traceability, resulting in inefficiency and potential compliance issues.
As a manufacturer of food service equipment, the manufacturer is required to comply with stringent National Food Safety (NFS) requirements, CE and UL marking requirements. In addition to their standard line of food service equipment, the company also provides food service equipment new product development to the restaurant industry (ie. chillers, warmers, dispensers).
Based on the current process and lack of documented practices, laboratory operations could not meet the projected goals and compliance was at risk.
Interviews were conducted with key stakeholders in the organization and the current state was evaluated. It was determined that many of the laboratory processes were not documented and analysis requirements were not defined. In addition, there was no standardized report formatting and the data storage was neither centrally located nor documented.
- Many of the laboratory processes were not documented. For example, the analytical testing request process was not defined and was not robust, resulting in inconsistent results.
- Documentation of processes is especially critical in analytical testing environments. Without documenting the processes, the processes are not repeatable and therefore, reduces the likelihood of producing repeatable results.
- There was no standardized report formatting and the data storage was neither centrally located nor documented. Laboratory scientists saved the data in various electronic locations.
- Standardized report formatting is important to efficiently compare analytical results. Without standardized report formatting, laboratory scientists may waste time by reviewing various data points or reports.
- By keeping the data centralized, data was easily accessible to the laboratory scientists and was available for evaluation and comparison. Maintaining separate locations decreased visibility and accessibility.
CLIENT COLLABORATION
Based on the client context and regulatory requirements, Total CI Info, LLC developed a SIPOC Model for the food equipment manufacturer to evaluate and better define the needs of the business and constraints of the laboratory process.
A SIPOC Model outlines a high-level view of a process, including: Suppliers, Inputs, Process, Outputs and Customers. In this model, suppliers provide inputs to a process. There are outputs to the process. These outputs are then delivered to Customers.
Based on interviews with key stakeholders, the SIPOC Model developed for the food equipment manufacturer is in Figure 1. SIPOC Model for Food Equipment Manufacturer.
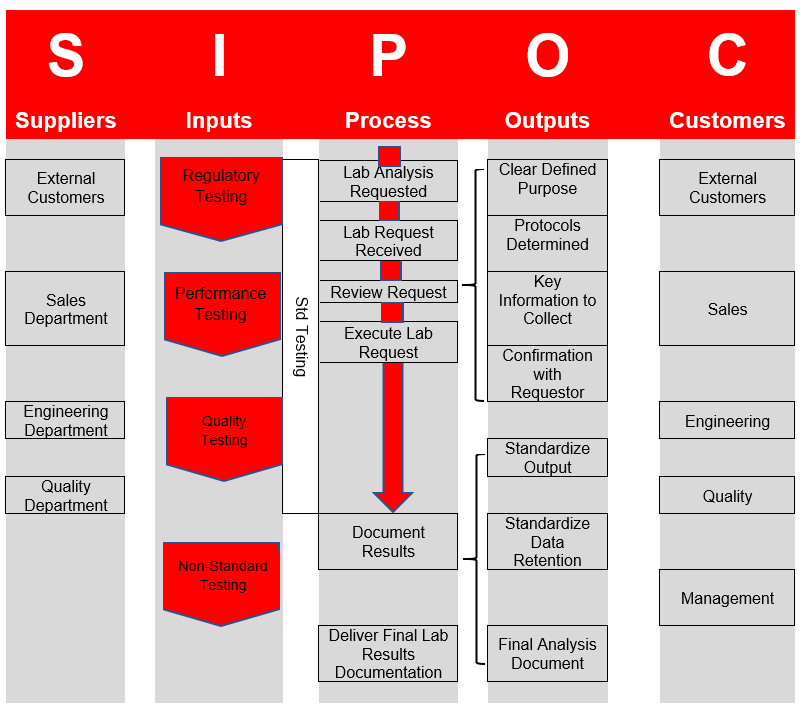
Figure 1. SIPOC Model for Food Equipment Manufacturer.
In evaluating the process, Suppliers, Inputs, Process, Outputs and Customers were identified. The suppliers to the process included external customers, sales, engineering and quality departments. The inputs to the process included regulatory, performance, quality and non-standard testing.
In defining the process, the laboratory analysis is requested, received and reviewed. The lab request is then executed and results documented. The final laboratory results are then delivered. There are various outputs to the process. For the review request, a clear defined purpose was needed. In addition, protocols were determined, key information to collect was identified, and request is confirmed. For the documentation of results, the outputs and data retention were to be standardized and results reported in a final analysis document. Impacted customers to this process included external customers, sales, engineering, quality and management.
CLIENT RESULTS
Creation of the SIPOC model resulted in the identification of processes to be created to help standardize the processes and to improve compliance. In addition, other continuous improvements were made, including the implementation of a communication tool, the Focused Request workbook. The Focused Request workbook included prompts for requested analysis. The implementation of the Focused Request workbook enabled the requestors to communicate testing needs to the laboratory staff. The Focused Request workbook also enabled the laboratory staff to prioritize the workload. Focused data entry screens (including adding documented procedure references) were also created for easy reference and access.
In addition, to improve database maintenance, an administration section was created to capture database recommendations (i.e. changes in customer requirements, test requirements and product requirements). A custom made database was developed to collect critical data points. These data points could then be used for process performance metrics (i.e. turnaround time) and enabled for improved functionality of report generation. Automated reporting features were also added, including an automated Excel report (including automated storage and filing formats) and Minitab graphs for easy visual analysis.
The SIPOC model can be a useful tool when evaluating a complex process, not only in the laboratory equipment industry, but in other industries, as well. As part of the SIPOC process, the Suppliers, Inputs, Process, Outputs and Customers were determined. Processes were identified and documented. In this case, the identification and documentation of processes resulted in improved traceability and overall compliance for the food service equipment laboratory. In addition, by documenting the processes, the overall efficiency of the laboratory was also improved. By keeping the data centralized, data was easily accessible to the laboratory scientists and was available for data evaluation and trending, resulting in data-driven decisions.
Considering defining a complex process? Add a SIPOC model to your continuous improvement tool box as a starting point for analysis of the process!
Leave A Comment